Author: Editorial board
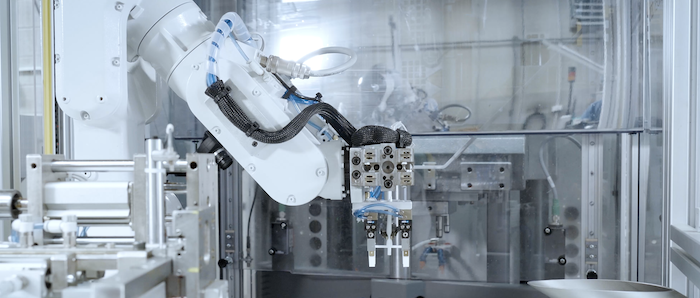
Automated moulding system: what is it?
A new machine has been introduced in our production plant for the automated production of 6.3x0.8mm faston supports by means of a co-moulding operation. This is the component that enables the electrical connection of the SLIM basic signalling units and panel light indicators. The entire production workstation consists of a vertical press, an anthropomorphic arm and an automated feeding system. Through precise start-up programmes, the machinery is able to produce different versions of this component.
The introduction of this automated workstation, which required the implementation of the Manufacturing Execution System (MES), was the first big step for SLIM in the Industry 4.0 perspective.
Are you interested in SLIM's product offer? Click on the button below and download the product catalogue, inside you can find all the technical sheets of the various components available.
The advantages of automated production
At the production level, this very fast and precise technical process eliminates the variability of the human component, thus leading to an increase in quality. Through precise settings and an advanced system of infrared viewers, the automated workstation performs accurate inspection. Specifically, it inspects to the millimetre that the metal parts are correctly positioned inside each seat or mould and that the entire automated production process is carried out in the specified manner. Thanks to this control system, it is impossible for the co-moulded support to fail. Therefore, with this process, you can be sure that no components are missing and that the plastic parts are complete. We opted to invest in this new 4.0 machine precisely because of the increased quality of the finished product and its repeatability.
The faston mount 6.3x0.8
The faston support is a component consisting of 2 metal terminals (male faston 6.3x0.8mm) embedded in plastic material and is used for the electrical connection of the indicator light to the rest of the wiring.
Faston: a definition
The faston component is a type of terminal used by the cable fitter to electrically connect a warning light or indicator light to the application on which it is used. Considering an indicator light seen from the outside and breaking it down into its main parts, we find in order: the lens or diffuser, the body of the indicator light and finally the final part formed by the faston supportt. In this last part, there are two metal plates through which the connection is made by inserting this metal component into a female faston 6.3x0.8mm.
Faston male 6.3x0.8mm in brass
In the metal terminal market, there are some standard sizes for this type of electrical connection. The mains ones are: faston 6.3x0.8mm, faston 4.8x0.8mm or even 2.8x0.5mm. These sizes must be such that the female connection used can be matched correctly. For this reason, SLIM has kept to the 6.3x0.8mm size, one of the most commonly used standard sizes for wiring with these terminals.
For the faston male 6.3x0.8mm in brass the material used for the metal body is brass. For the co-moulded plastic part, on the other hand, it is possible to choose between different colours and polymers. Depending on the desired colour, a special moulding programme will be selected, based on specific parameters that influence how best to melt the polymer. Not all components follow the same manufacturing process, but different programmes have been created in relation to the moulding material. But how does the production of fastons take place through the automated production workstation? Find out in the video below!
Faston mount 6.3 and its production
The 4.0 machine consists of a vertical injection moulding machine, manufactured by ARBURG, and a complex automation system. DRAKAR Automation by SVERITAL was responsible for the design and assembly of the automation components of our production workstation, including: vibrator, handling system, linear feed system, anthropomorphic arm and the complex vision system for process and finished component control.
The vibrator and the linear movement system in this automated moulding system bring the metal terminals (male faston 6.3x0.8mm in brass) into an insertion jig. At this point, the anthropomorphic arm picks up the metal terminals and inserts them into a mould positioned on a turntable. The table then rotates 180° and brings the mould into the injection chamber of the machine. At the end of this procedure, you will have 4 complete faston mounts.
A faston support made by such a co-moulding process is certainly more solid and compact than the same component obtained by mechanically inserting and locking the fastons inside the previously moulded plastic support.
Would you like to receive more information on SLIM solutions? Click on the button below and feel free to contact us!