If you want to learn more about SLIM collaborations that led to innovative lighting solutions click the button below.
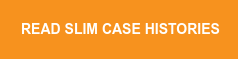
A LED microcircuit for multiple applications
In 2020 Luxelt designed and produced the smallest LED circuit ever made, which at SLIM we are using for the new series of micro spotlights : this is a flexible system that easily adapts to the needs of our customers in different production sectors, such as manufacturers of coffee machines, equipment for the food industry (ovens, hoods, hobs) and vending machines. We turned to Luxelt for the supply of the Microlight electronic circuit mainly because of its high efficiency and small size, which proves to be a winning combination that ensures the ideal adaptation to the final products.
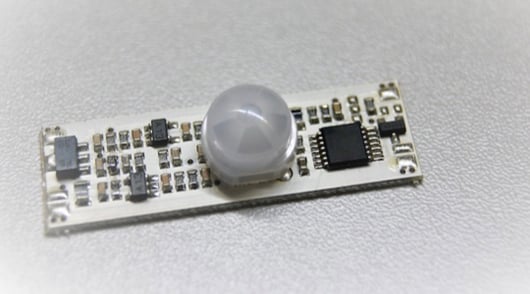
Initially, we asked Luxelt for samples that were useful for a broader evaluation of the product, which highlighted the following benefits:
- quick insertion by the customer in their final application;
- customization that we can carry out on our case according to customer needs;
- low consumption of the LED source in relation to its luminous efficacy;
- low working temperatures of the LED circuit;
- low costs that allow us to satisfy a wider range of customers
These first samples have allowed us to work on the standard plastic case, which can always be customized to suit the application in the best possible way.
Furthermore, we have water-proofed the micro spotlight so that it can be inserted in all those applications where it is not possible to guarantee the absence of water or moisture at the point of application, both during the operation or the stand-by phase, or during transport and storage.
A LED microcircuit born from a synergy
SLIM and Luxelt collaborated on a project for lighting solutions that began with feasibility studies, which were carried out starting from the analysis of the client's needs, through the research and verification of correspondence with the regulations in force, and continued with the processing of the masters for printed circuits. Subsequently, prototypes were made, to give customers the opportunity to verify the quality of the products.
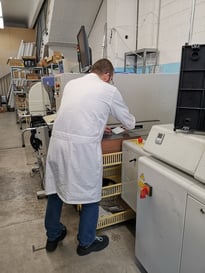
Following the approval of the prototypes, we started the production: any electronic circuit is assembled in-house, both with traditional components and with SMD (Surface Mounting Device) components, thanks to the use of a new automatic line consisting of a screen printing machine, a pick & place device and an oven. All this guarantees quick production times, the quality of the product and the reduction of risks and costs.
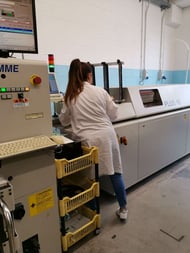
Finally, tests and inspections were carried out on each resulting product by way of visual inspections, electrical-functional testing, insulation and conductivity tests.
A synergy of companies to make the most of the potential that comes from years of experience!
For further information, click on the button below and write to us!
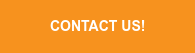