SLIM (Società Lampade Interruttori Mercurio) was founded in 1973 by six people with a strong mechanical and electrical engineering background. The company started out producing neon lamps with glass bulbs and electromechanical switches.
In line with the company's interest in technological innovations, in 1974 the production line was enhanced by the addition of moulding presses for plastic components, which fostered an increase in the production.
The story behind SLIM S.r.l.
In 1975 SLIM took part in the first trade fair in Milan, which was followed by the foreign trade fairs in Cologne, Paris, Hannover, and Madrid. The subsequent acquisition of the company VETO fostered an increase in the production of switches.
On the back of a consolidated commercial network in Italy and abroad, and attentive to market innovations, in 2000 SLIM began to integrate LED technology in the production of indicators.
Today, the second generation at the helm of the company faces a new phase characterised by change and innovation.
Click on the button below in order to discover more about today's company reality!
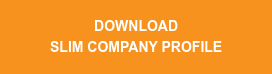
SLIM S.r.l.: towards a bright future
SLIM is preparing for the future, drawing its strength from 45 years of tradition and experience, and from a company management that has a clear mission and vision: always anticipating customer's requests and offering lighting solutions, which are increasingly performing and adapt to the spirit of the times.
The market, in fact, constantly puts forward new challenges: SLIM designs innovative solutions and customized products, perfecting current technologies and implementing future ones, with a constant commitment to meet customers' needs.
The projects that SLIM takes on are stimulating challenges that push us to relentlessly fine-tune and innovate the company.
SLIM - Our research and development sector
Research is the basis of our work. The production applications are numerous. Light indicators are components that are used in various market sectors: from household appliances (washing machines, television sets, ovens and fridges) to the HO.RE.CA sector; from lighting to home automation, to the electro-medical sector; from the HVAC sector to automotive.
LED technology joins the now consolidated neon solution and pushes towards new scenarios, such as optical fibre and other forms of lighting.
SLIM's value chain for its customers consists in 4 stages:
- Stage 1 - moulding. 13 presses produce all the plastic components used in our product range;
- Stage 2 - crimping and welding. The components undergo the first stages of the production process;
- Stage 3 - assembly. In this stage, the experience gained over the years by our operators proves to be fundamental. The success of the final piece depends above all on this stage.
- Stage 4 - testing. This crucial part of the production process is synonymous with guarantee on our products, a distinctive feature that makes SLIM stand out in the market for quality and reliability of results.
SLIM's production system represents the company's daily commitment in the production of lighting solutions. Our aim is to be increasingly more efficient and to constantly improve the quality of the products.
Do you want to tell us about a project you have in mind? Click on the button below and write to us.
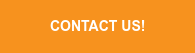